Manufacturing Methods of Industrial Pipe
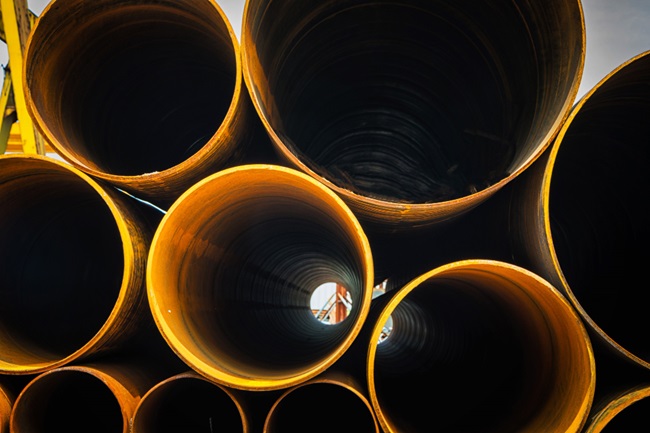
Manufacturing Methods of Industrial Pipe
- Industrial pipes are essential components in various industries, including oil and gas, power generation, water treatment, and chemical processing.
- The manufacturing process of industrial pipes is crucial in determining their strength, durability, and resistance to environmental factors.
Consider the following
- Carbon steel pipe can be manufactured using several different techniques.
- Each of these produces a pipe with certain characteristics.
- These characteristics include strength, wall thickness, corrosion resistance, and temperature and pressure limitations.
- For example, pipes having the same wall thickness but manufactured by different methods may vary in strength and pressure limits.
- The manufacturing methods we will mention include seamless, butt-welded, and spiral-welded pipe.
Common Manufacturing Methods of Industrial Pipes
1. Seamless Pipe Manufacturing
Process
-
- A solid cylindrical billet is heated and pierced to create a hollow tube.
- The tube is elongated and shaped using rotary or extrusion processes.
- It is further refined to achieve the desired thickness and diameter.
Advantages
-
- Higher strength due to the absence of welded seams.
- Greater resistance to high pressure and temperature.
- Superior uniformity and smooth interior surface.
Applications
-
- High-pressure applications in the oil and gas industry.
- Boiler tubes and heat exchangers.
- Aerospace and automotive sectors.
2. Electric Resistance Welded (ERW) Pipes
Process
-
- A steel strip or coil is passed through forming rolls to create a cylindrical shape.
- The edges are welded together using high-frequency electrical resistance.
- The pipe is then cooled, sized, and cut to length.
Advantages
-
- Cost-effective and efficient for large-scale production.
- Suitable for standard pressure applications.
- Available in various diameters and thicknesses.
Applications
-
- Water pipelines and distribution systems.
- Structural and construction applications.
- Fencing and scaffolding.
3. Submerged Arc Welded (SAW) Pipes
Process
-
- A steel plate is rolled into a cylindrical shape.
- Welding is performed using an electric arc submerged under a blanket of flux.
- The pipe is then inspected, tested, and coated if necessary.
Variants
-
- Longitudinal Submerged Arc Welded (LSAW) – Weld seam runs longitudinally.
- Spiral Submerged Arc Welded (SSAW) – Weld seam follows a spiral path.
Advantages
-
- Strong and reliable welds.
- Suitable for large-diameter pipes.
- Effective for high-pressure transportation.
Applications
-
- Oil and gas pipelines.
- Structural applications in bridges and buildings.
- Water transmission pipelines.
4. Casting Method for Pipes
Process
-
- Molten metal is poured into a mold to create the desired pipe shape.
- The mold is cooled and removed to obtain the solidified pipe.
- Finishing processes, such as machining and coating, are applied.
Advantages
-
- Can produce complex shapes and large pipe sizes.
- High resistance to corrosion and wear.
- Suitable for bulk production.
Applications
-
- Ductile iron and cast iron pipes for sewage and water systems.
- Chemical industry applications.
- Underground pipelines.
5. Extrusion Method for Plastic Pipes
Process
-
- Polymer pellets are melted and forced through a die to create a continuous pipe shape.
- The extruded pipe is cooled and cut to the required length.
- Additional treatments, such as reinforcement or lining, may be applied.
Advantages
-
- Plumbing and drainage systems.
- Chemical transportation.
- Agricultural irrigation systems.
Applications
-
- Plumbing and drainage systems.
- Chemical transportation.
- Agricultural irrigation systems.
6. Forged Pipe Manufacturing
Process
-
- A metal billet is heated and shaped using compressive forces.
- The pipe is then machined to achieve precision dimensions.
- Additional heat treatment may be applied to enhance strength.
Advantages
-
- High mechanical strength and durability.
- Resistance to high pressure and impact.
- Used in critical applications requiring reliability.
Applications
-
- High-pressure steam and gas pipelines.
- Hydraulic and mechanical systems.
- Aerospace and defence industries.